The Future of
Automation for CONTAINER CLOSURE INTEGRITY TESTING
Authors: Oliver Stauffer & Noba Ebaid
The FDA continues to encourage the shift away from a
compliance culture to one that is of a more holistic quality mindset
in the manufacturing realm. The topic of quality assurance has never
been more dynamic. Multiple guidance documents weave a strong fabric
of quality frameworks. One topic that has garnered specific attention is container
closure integrity. An integral container is the single most critical attribute to protect product quality beyond the
walls of manufacturing. CCI is a critical quality attribute (CQA) for parenteral product classes, dictating a high
level of risk mitigation.
In recent years, regulatory bodies and guidance documents have been prompting the industry to adopt
deterministic CCIT technologies and discourage traditional, probabilistic approaches. At a foundational level,
probabilistic methods do not have the measurement and control capabilities needed for modern validation
requirements. For quality attributes as high risk as CCI, greater levels of control are needed. New regulatory
guidance documents continue to tighten the narrative on what is expected of container closure integrity.
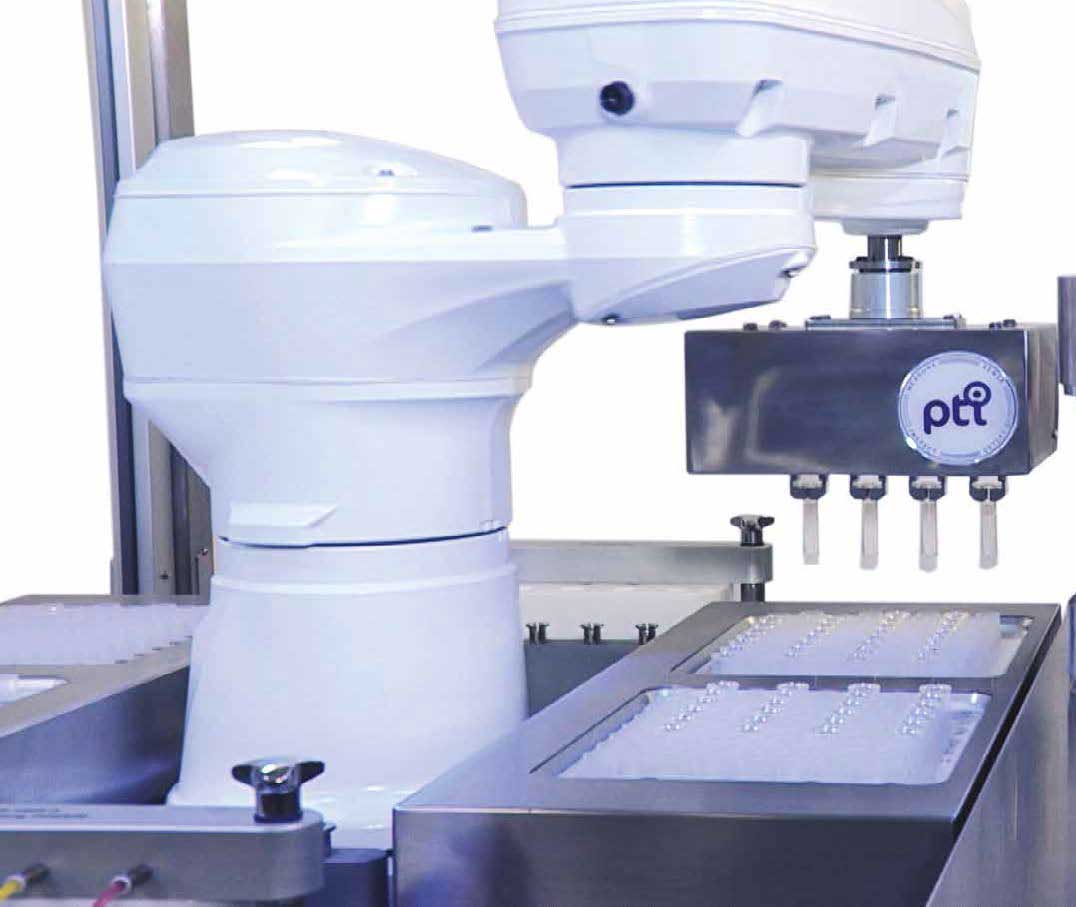
An international consortium of regulatory bodies, PIC/S, worked to update EMA’s Annex 1, the latest in a series
of regulatory guidance aimed at quality. The document has very specific requirements to assure CCI and calls
for scientifically justified test methodology and sampling plans to assure CCI commensurate with the level of
risk. Other prominent bodies (USP) are also prescribing deterministic methods while outlining the need for a
scientific understanding of the package and contents. This is particularly relevant considering that more effective
technologies and resources are readily available for the industry to adopt. For most container formats there is
no regulatory guidance dictating that 100% of units should be inspected. There is regulatory guidance for all
parenteral inspection applications to achieve greater sampling rates using deterministic technologies. In this
case, an automated approach to integrity testing that is deterministic, quantitative, and objective is an extremely
effective approach to achieving quality objectives.
The final fill-finish process has a significant set of input variables that impact container closure integrity.
All roads point to increased frequency of more controlled test methods: automated CCIT. While regulatory
protocols have been established, they are not always perfectly clear. For example, it is a common misconception
that 100% inspection of all product types is a requirement, or that it is the most effective path forward. The
reality is that increasing inspection frequency does improve assurance, but not if it means forgoing capability
to detect all CQA’s. Inspecting 100% of product at typical production rates typically requires forgoing some
level of sensitivity or performance.
100% inspection is often seen as the optimal level of inspection, but it comes at a cost to quality. Effective
product inspection requires time and control, often difficult to achieve at high production speeds. If an
inspection solution is directly integrated into 100% of the product flow, the detection performance is often
diminished for the sake of maintaining line speeds. It can also be an unnecessary hindrance to production,
halting throughput if delicate sensory measurement components are not cooperating. Deploying automated
statistical process control instead places the focus on CQA’s and resolves the primary issue with 100% inspection:
diminishing inspection performance for the sake of 100% throughput. Inspection can be a delicate process, and
above all, should be a process that is allotted the time that it takes to effectively inspect for CQA’s. Anything
less and a QRM assessment would show unmitigated risk. The optimal solution is a decoupled automated
inspection solution that inspects a scientifically appropriate sample quantity.
Adjusting the quality levels that are deemed acceptable for an inspection method to match certain production
line speeds will only serve to reduce quality. Inspection methodology can focus squarely on CQA’s, and
production throughput can continue uninhibited. Scientifically effective sampling plans provide assurance
that production lots are free from systematic quality issues, and the inspection can provide assurance that
CQA’s are met. Deploying at-line automated inspection solutions that are decoupled from the production line
allows for the inspection process to prioritize product quality.
Increasing inspection frequency reaches optimal detection capability based on batch size, peaking at 1250
samples tested per batch based on Squeglia’s model of zero acceptance sampling plans. Beyond the quantity
of inspection, there is theoretically no greater level of assurance provided by testing more samples, and testing
at higher frequency, by default, limits the level of inspection capability. The optimal inspection method inspects
for defects that align with CQA’s while also providing the highest level of assurance. To achieve this, a test
method must be developed to detect defects down to the CQA’s of the product. Then the test method must be
increased in frequency to the greatest extent possible to achieve the highest level of assurance. Approaching
the challenge in the opposite order will likely result in selecting a 100% inspection approach that provides a
high level of assurance in detecting only a limited set of critical defect modes.
When considering statistically valid inspection frequencies, understanding the approaches relating to sample/
batch size is critical. Based on peer reviewed articles and new industry guidance, it is clear that risk-based
approaches are required. The most critical documents for pharmaceutical containment quality today are USP
1207, EMA’s Annex 1, and ICH Q8 & Q9. Together these documents assert a need for improved quality risk
management, scientific justification in mitigating risk, and a scientifically justified sampling plan.
The combination of deterministic CCIT methods and automation represents a significant opportunity to achieve
critical quality improvements in alignment with those four regulatory guidance documents. Striking the right
balance between inspection frequency and detection capability is crucial for optimizing assurance levels.
Deterministic technologies provide reliable and scientifically validated results. A deterministic CCI method
is the most accurate means to assure the sterility of a product beyond the walls of the fill-finish operation.
Automation enhances practicality, reliability, and the ability to meet sample testing efficiency to align with
scientifically valid sampling plans. As the industry continues to prioritize quality, the integration of automated
statistical process control with deterministic CCIT methods will be pivotal in meeting the evolving demands of
pharmaceutical manufacturing.
REFERENCES